Comprehensive Guide: What is Porosity in Welding and Exactly How to avoid It
Comprehensive Guide: What is Porosity in Welding and Exactly How to avoid It
Blog Article
Porosity in Welding: Identifying Common Issues and Implementing Finest Practices for Avoidance
Porosity in welding is a prevalent problem that often goes undetected up until it causes substantial issues with the integrity of welds. In this conversation, we will explore the vital elements contributing to porosity development, examine its destructive impacts on weld performance, and review the finest techniques that can be embraced to minimize porosity event in welding processes.
Usual Root Causes Of Porosity

Utilizing unclean or damp filler products can present impurities into the weld, contributing to porosity problems. To alleviate these typical reasons of porosity, thorough cleaning of base metals, proper protecting gas choice, and adherence to ideal welding criteria are crucial practices in achieving top quality, porosity-free welds.
Effect of Porosity on Weld High Quality

The existence of porosity in welding can considerably compromise the structural honesty and mechanical residential or commercial properties of bonded joints. Porosity creates gaps within the weld steel, deteriorating its overall toughness and load-bearing ability.
One of the primary effects of porosity is a reduction in the weld's ductility and strength. Welds with high porosity degrees have a tendency to exhibit reduced effect strength and lowered capability to deform plastically prior to fracturing. This can be especially concerning in applications where the bonded components undergo dynamic or cyclic loading problems. Moreover, porosity can hinder the weld's capacity to successfully transmit pressures, resulting in early weld failure and possible security threats in vital structures.
Ideal Practices for Porosity Prevention
To improve the architectural integrity and high quality of bonded joints, what specific steps can be carried out to minimize the occurrence of porosity throughout the welding procedure? Porosity prevention in welding is vital to ensure the stability and toughness of the last weld. One effective method appertains cleansing of the base steel, removing any pollutants such as corrosion, oil, paint, or dampness that can lead to gas entrapment. Guaranteeing that the welding tools is in great problem, with clean consumables and proper gas circulation prices, can also dramatically reduce porosity. Furthermore, preserving a stable arc and managing the welding specifications, such as voltage, present, and take a trip rate, aids develop a regular weld swimming pool that minimizes the risk of gas entrapment. Making use of the proper welding technique for the certain product being bonded, such as changing the welding angle and weapon setting, can additionally stop porosity. Normal examination of welds and prompt removal of any type of problems determined during the welding process are important methods to avoid porosity and produce premium welds.
Significance of Proper Welding Strategies
Executing proper welding strategies is critical in ensuring the architectural integrity and top quality of welded joints, building on the structure of effective porosity avoidance steps. Welding strategies directly her explanation influence the general toughness and toughness of the welded framework. One key element of proper welding methods is maintaining the right heat input. Extreme heat can cause increased porosity because of the entrapment of gases in the weld swimming pool. On the other hand, not enough warm might result in incomplete blend, creating possible weak points in the joint. Furthermore, making use of the suitable welding criteria, such as voltage, current, and travel rate, is crucial for accomplishing audio welds with minimal porosity.
In addition, the selection of welding process, whether it be hop over to here MIG, TIG, or stick welding, should align with the particular demands of the job to make certain optimum outcomes. Proper cleaning and preparation of the base metal, as well as choosing the best filler material, are likewise necessary parts of skillful welding strategies. By sticking to these ideal techniques, welders can minimize the risk of porosity development and generate high-quality, structurally sound welds.
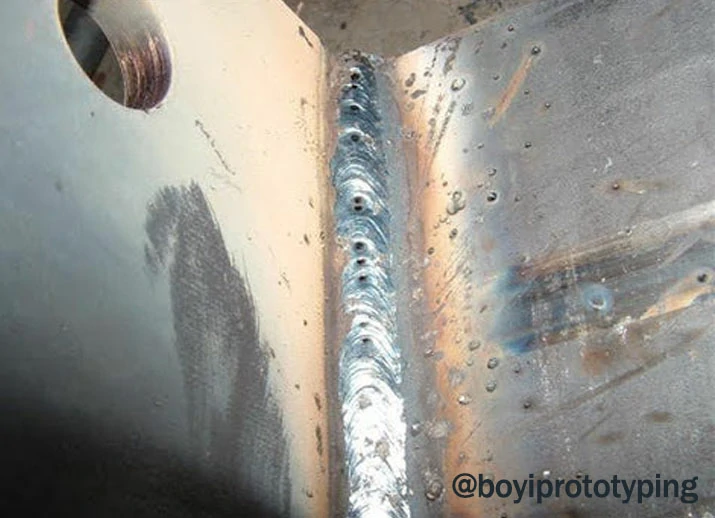
Examining and Top Quality Control Measures
Quality control procedures play a critical duty in verifying the integrity and reliability of welded joints. Evaluating procedures are important to identify and protect against porosity in welding, ensuring the strength and resilience of the final product. Non-destructive testing methods such as ultrasonic testing, radiographic testing, and visual inspection are commonly employed to identify possible issues like porosity. These strategies permit the analysis of weld top quality without endangering the stability of the joint. What is Porosity.
Post-weld examinations, on the other hand, examine the last weld for any flaws, including porosity, and verify that it fulfills defined standards. Carrying out a comprehensive high quality control strategy that consists of extensive screening treatments and inspections is vital to lowering porosity issues and guaranteeing the click resources general top quality of welded joints.
Conclusion
Finally, porosity in welding can be an usual concern that impacts the quality of welds. By determining the typical sources of porosity and applying best practices for prevention, such as appropriate welding methods and screening actions, welders can ensure excellent quality and dependable welds. It is vital to focus on avoidance approaches to minimize the occurrence of porosity and maintain the integrity of welded structures.
Report this page